关键词:内燃机车;,车轴:疲劳裂纹;疲劳断裂;轮对;故障;措施
东风4型内燃机车轮对是由车轴、从动齿轮、长毂轮心、短毂伦心、轮箍等组成。它是走行部中最重要的部件,它在运行中承受着复杂的交变载荷作用。因此轮对会出现一些危及行车安全的故障,车轴疲劳裂纹、轮箍驰缓等。下面分析一下产生车轴疲劳裂纹和轮箍驰缓的原因及解决措施。
一、车轴疲劳裂纹
车轴产生疲劳裂纹的原因是多方面的。既受车轴材质、结构、制造工艺、牵引电机和轮对参数选配等因素的影响,又受机车运用线路、运行速度、牵引吨位以及司乘人员操作情况等因素的影响。由于受力特点,受力状态,工作环境不同,车轴在运用过程中受到弯曲应力,扭转剪切应力及组装应力的同时作用,其产生疲劳裂纹的原因是相当复杂的,是在几种因素综合作用下产生的。
车轴疲劳断裂由以下4个过程组成
1、裂纹源形成:深度较浅的一个或几个腐蚀坑长期在集中应力的作用下,逐渐在其周围产生轻微疲劳裂纹,形成裂纹源。
2、疲劳核形成:车轴在交变弯曲应力作用下,裂纹源处首先发展并逐渐扩大,形成疲劳核,其表面光滑。当应力幅达到最大值,裂纹就向前推进一级,在此期间(也称慢速发展期)裂纹发展缓慢,稳定扩展。
3、快速发展期:
当裂纹发展到一定程度时,应力不断作用在裂纹处,使疲劳裂纹不断发展。由于应力受使用条件的影响时大时小,因此疲劳裂纹的发展断面为波浪状,称贝壳状。当应力达到最大时疲劳裂纹就向下发展一级,当应力达到最小时疲劳裂纹就停止发展,形成疲裂纹中止线,在此期间裂纹发展非常快。
4、脆断:当车轴裂纹处的有效承载面逐渐缩小至不能承担最大应力时;发生一次性断裂。
东风4型内燃机车车轴疲劳裂纹的产生有以下几个原因
1、经探伤检查出的轮对疲劳裂纹均发生在车轴长毂轮座上距侧轴端640~65 0 mm处(见图1),裂纹呈沿圆周方向不连续点状或连续周线,深度O.3~5mm不等。
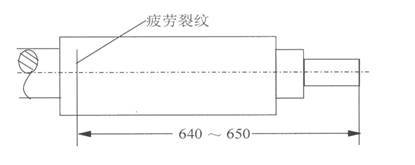
图1 车轴裂纹分布
2、车轴装配面轴向应力分布特点显示,在车轴长毂轮座产生应力集中,易发生疲劳裂纹(见图2)。
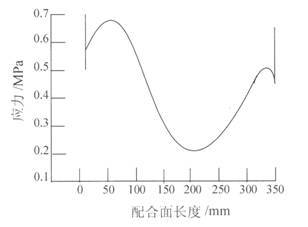
图2车轴装配面轴向应力分布
3、由于采用单齿传动结构,轮对在传递动力过程中车轴承受巨大的扭矩,其中机车起动时的扭矩为运行中的好几倍。两边镶入部同时受变弯曲应力的作用,由于扭矩的影响使齿轮一侧的应力加
大,裂纹产生率要比非齿轮侧高得多。
4、轮对装配过程中,直接压装法在车轴长毂轮座上距轴端640~65 0mm处产生“挤堆”现象,形成裂纹源。在探伤时发现的假裂纹就是这“挤堆”现象造成的。
5、直接压装法和注油压装法在车轴压装过程中所产生的擦伤腐蚀,降低了车轴表面粗糙度,并降低了车轴的疲劳强度。
6、轮对主从动齿轮磨损造成啮合状态的恶化,机车减振系统效率降低时所产生的蛇行运动,轮箍踏面严重擦伤、剥离所导致的轴重再分配,均增加了车轴所受的冲击和交变载荷,降低了车轴的
疲劳寿命。
解决措施:
1、高度重视车轴的疲劳裂纹
目前,各段车轴超声波探伤水平参差不齐,据调查有的机车段极少发现车轴的疲劳裂纹甚至从未发现过车轴的疲劳裂纹。由于检修规程中允许车轴在有轻微疲劳裂纹的情况下可实施监测。我段以前就采取对疲劳裂纹实施监测的简单方法。但经过多次验证,我们发现用超声波方法检测出的疲劳裂纹深度是很不准确的,况且当轴的疲劳裂纹超过一定限度时发展速度非常快,严重危及行车安全。因此我们必须以科学的态度,安全第一的思想高度重视车轴的疲劳裂纹,特别是在列车提速的今天更应重视。
2、采取科学的超声波探测方法,不断提高超声波的探测水平。
对东风4型机车车轴进行疲劳裂纹超声波探伤可以用透声检查、小角度纵波探伤和斜探头横波探伤等3种方法,还可以对探出有裂纹的轮对进行解体再确认裂纹有无、裂纹深度、裂纹位置等。
如此反复进行,不断提高探伤人员识别车轴裂纹的水准。
二、轮箍驰缓
作为轮轨接触的基础部件,轮箍承受着复杂的交变应力,其工作应力、内应力、热应力,冲击力等叠加合成的单峰应力值是很大的。因此,分析研究轮箍驰缓的原因,必须根据轮箍的特点、工作条件、受力情况,从轮箍本身内部因素和机车运行的客观条件两方面来进行。
l、轮箍本身的内部因素:
①、轮箍材质存在缺陷
②、轮箍嵌装时过盈量不足,或新箍减薄后过盈量减小。
③、经机械加工后的轮心外径和轮箍内径面,其圆度、圆柱度、粗糙度等不符合规定要求
④、机车运用,检修过程中轮箍受了机械外伤。调查结果表明:发生踏面剥离的机车大都轮箍较厚,而发生轮箍松驰、窜出的机车大都轮箍相对较薄。经进一步分析,有些厂家生产的轮箍在材质方面存在一些质量问题(如金属组织内部缺陷,耐磨性差等),但对于轮箍与轮心的结合并无影响,轮箍厚度原形76mm中修后不少于45mm,定修后不少于38mm,过盈量按1000mm轮心直径为1.2~1.5mm计算,东风4型机车轮心直径为900mm,过盈量应为1.08~1.35mm,新轮箍的过盈量一般按1.35mm掌握,经旋削或磨耗减薄后,过盈量会相应减小,在对一些发生驰缓的轮箍进行退箍检查时发现,除了少数轮箍的过盈量不足外,其过盈量及机械加工精度,粗糙度等大都符合规定要求。因此对发生轮箍驰缓的情况进行分析,可以认为,其主要原因不是轮箍本身,在过盈量符合规定的条件下,轮箍的厚薄对制动热量的散热面积和传递速度有较大影响。
2、从轮箍的工作条件下分析
①工作者对机车基础制动装置的维修保养工作缺乏足够的认识,存在的质量问题较多,如轴箱拉杆橡胶套破损后使车轴中心线偏离正常位置,导致少数车轮在运行中长时间制动发热,以致造成轮箍驰缓,这是当前轮箍驰缓的主要原因。而导致长时间制动发热的因素有:①、闸缸勾贝行程及闸瓦间隙调整偏小,造成个别车轮与闸瓦帖靠运行。
②、机车在运行中未松手制动装置。
③、基础制动装置维修保养差,技术状态不良,造成制动勾贝,复原弹簧,调整器及制动各杆动作不灵活,发生卡滞现象。
④、机车轮对发生空转,特别是多次,较长时间的空转。⑤、轴箱拉杆橡胶套材质老化,弹力不足或者破损,使轴箱的纵向定位失效,轴距发生变化。由于轴箱拉杆橡胶套嵌装部的内径与心轴外径的直径差为15mm,所以橡胶套破损后,轴距的变化可达7.5~15mm,远大于闸瓦间隙6~8mm,在这种情况下,会产生车轮“主动”贴靠闸瓦的现象,造成轮箍发热驰缓。
防止措施
1、执行统一的闸缸勾贝行程技术标准,无论运用机车还是检修机车,一律按74~123mm执行。同时,要求将闸瓦间隙调整为6~8mm。
2、制订基础制动装置的使用技术条件。①、制动缸和制动各杆,无论在制动或缓解状态均不得有卡滞现象,基础制动装置各零部件必须安装牢固,位置正确,润滑良好,作用正常。②、闸瓦间隙调整器螺杆及转盘应转动灵活,不得卡滞,棘瓜应正确地卡在棘轮上。③、闸缸勾贝行程为74~123mm,闸瓦间隙为6~8mm,各连结销套的间隙必须符合《段规》要求。④、闸瓦上下方的间隙应调整一致,并不得磨轮缘。⑤、检查闸缸勾贝行程时,闸缸压力应为O.3MPa,为便于观测各闸缸勾贝行程的实际数值,可在每个闸缸前盖靠转向架一侧装设勾贝行程标尺。
3、加强机车出入库的管理工作①、乘务员必须按规定的岗位职责检查基础制动装置及轮箍状态。确保其状态符合技术条件。②、乘务员在更换不良闸瓦后,必须调整闸缸勾贝行程。检查闸瓦间隙时,应以闸瓦与轮箍踏面距离最近处为准,同时向制动装置各磨擦面给油。
③、机车出库牵引列车前,乘务员必须先松手闸,并确认手闸全松,手闸摇把的旋转方向必须打印清晰的油漆标记。④、机车出库前及中途运行停站时,乘务员必须在施单阀缓解后,检查确认闸缸勾贝是否全部复原,闸瓦是否离开车轮。
4、重视检修及保养工作
①、将基础制动装置及闸瓦间隙调整器的检修纳入定修范围。
②、机车中修时,轴箱拉杆橡胶套必须全部更换新品,定修时,应加强检修,及时更换不良品。
③、重新涂印模糊不清的轮箍弛缓标记。
④、机车检修时,乘务员必须对基础制动装置进行给油。
⑤、更换轮箍时,要检查确认轮心外径及轮箍内径面的加工精度、粗糙度、科学合理地计算过盈量,旧轮箍退下再用时,必须进行严格探伤。
⑥、在检修过程中,加强闸瓦间隙自动调整器棘瓜弹簧的检修。
⑦、加装轮箍驰缓报警装置。了解掌握了轮对的构造原理及在运用中存在的不良状态后,我们可以从个个方面对不良状态进行分析提出一些具体的解决措施,并在日常机车检修中加以运用,以提高机车检修质量,保证行车安全。
发表评论